Implantologia funzionale
L’implantologia funzionale consiste in una tecnica implantologica che si pone in accordo con la tendenza moderna della chirurgia che diventa ogni giorno meno invasiva. Questo significa meno sofferenza e più benefici funzionali immediati per il paziente.
Essa permette di adattare la struttura implantologica alle caratteristiche anatomiche del paziente che, salvo rari casi, non richiede quindi chirurgia preparatoria che utilizza a volte tecniche di trasposizione di osso da altri distretti anatomici.
L’ atraumaticità che contraddistingue l’implantologia funzionale la fa prediligere come tecnica di primo impiego lasciando come seconda scelta – e solo in caso di fallimento – le tecniche più invasive. Del resto, il fallimento a breve e lungo termine, date le caratteristiche tecniche del tipo di impianti, comporta delle piccole lesioni all’apparato osseo che va incontro a riparazione spontanea per cui può essere ripetuta a breve scadenza.
La solidarizzazione degli impianti fra loro comporta poi un differente modo di distribuzione delle forze agenti sulla struttura che perde quindi l’individualità di ogni singolo impianto e partecipa invece con un mutuo lavoro al sostegno meccanico della protesi.
Nelle seguenti figure si mostra un confronto tra una struttura complessa elettrosaldata ed un impianto tradizionale.
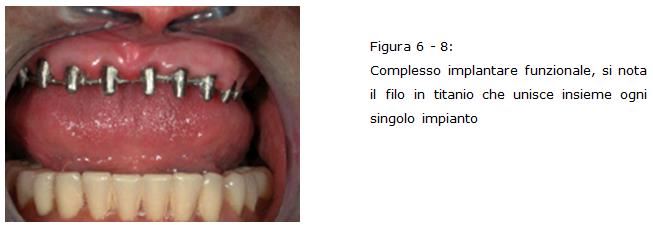
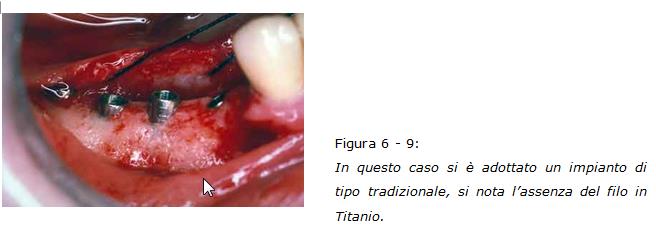
Caratteristiche generali
L’apparecchiatura permette di effettuare la saldatura direttamente nel cavo orale del paziente.
Il processo di saldatura è di tipo elettrico senza apporto di materiale in atmosfera di gas inerte in accordo con i principi enunciati da Lorenzon. Tra i due elettrodi della pinza vengono posizionati i due elementi da saldare. L’energia contenuta in una batteria di condensatori, precedentemente caricati, viene trasferita agli elettrodi della pinza, la corrente che fluisce attraverso i punti di contatto tra le due parti da saldare scalda il materiale fino al punto di fusione realizzando il giunto saldato.
Durante il ciclo il punto di fusione è protetto tramite l’apporto di gas Argon. Ciò evita che la zona di fusione, per effetto della temperatura possa reagire con l’Ossigeno contenuto nell’aria producendo ossidazione e quindi decadimento delle caratteristiche meccaniche del materiale utilizzato.
Il calore prodotto non raggiunge livelli pericolosi in quanto viene dissipato attraverso gli elettrodi sfruttando la maggior conducibilità termica del Rame.
Durante la fase di saldatura la pinza viene scollegata automaticamente dalla rete elettrica.
La saldatrice ha all’interno un microcontrollore che gestisce l’interfaccia utente tramite i tasti, l’encoder ed il display; la macchina è reimpostata a seconda dei calibri degli elementi da unire in modo darealizzare il processo con modalità e temporalità adeguate.
Il ciclo di saldatura è suddiviso in 3 differenti fasi, definite come:
1. Fase di pregas: emissione di argon in grado di assicurare che l’atmosfera nel punto di saldatura sia libera da ossigeno prima di iniziare la fase di saldatura.
2. Fase di sinterizzazione seguita dalla sincristallizzazione profonda: percentuale di energia erogabile agli elettrodi; ottenuta con il passaggio di corrente in grado di attuare l’eccitazione molecolare con variazione dei lagami atomici del Ti.
3. Fase di postgas: è necessaria che l’atmosfera sia libera da Ossigeno finché la temperatura del giunto non abbia raggiunto un livello tale di stabilità molecolare da evitare ogni possibile reazione con l’Ossigeno contenuto nell’aria.
Prima di ogni ciclo di saldatura il microcontrollore verifica che ci siano le condizioni corrette del circuito elettrico e del punto di saldatura.
Ciò significa che la resistenza elettrica del circuito complessivo deve essere inferiore ad un valore prestabilito. Inoltre un avvisatore acustico avvisa l’operatore dell’inizio e della fine del ciclo di saldatura.
Lo strumento è contenuto in un apposito contenitore che ne permette la trasportabilità.